Leveraging AI to Improve Fabrication Time Estimates
SJC Hutchinson Engineering specialises in manufacturing metal structures and components, serving the automotive, crushing, screening, and agricultural sectors. The company operates advanced machinery, including CNC lasers, press brakes, lathes, and mills, across over 40 fabrication bays to deliver high-quality solutions for its diverse client base.
The Challenge
SJC Hutchinson Engineering faces challenges in accurately estimating fabrication times, which impacts operational efficiency and profitability. The company struggles with bottlenecks, downtime, and inefficiencies in the fabrication process. Inaccurate time estimates, underquoting, and persistent issues such as incomplete kits and missing tools further hinder productivity. Existing methods, like lean cost modelling, require extensive engineering hours and offer limited accuracy, prompting Hutchinson to explore AI solutions for improved estimation processes and better data insights.
The Solution
To address challenges in estimating fabrication times and improving operational efficiency, SJC Hutchinson Engineering partnered with the Hartree Centre Northern Ireland Hub to develop a machine learning model that predicts fabrication times based on output quantity and skill level. The solution leveraged historical production data, with techniques such as data visualisation, feature engineering, and outlier removal. Three regression models were tested, with Random Forest proving to be the most effective for accurate predictions. This collaboration enabled better estimation and identification of bottlenecks in the fabrication process.
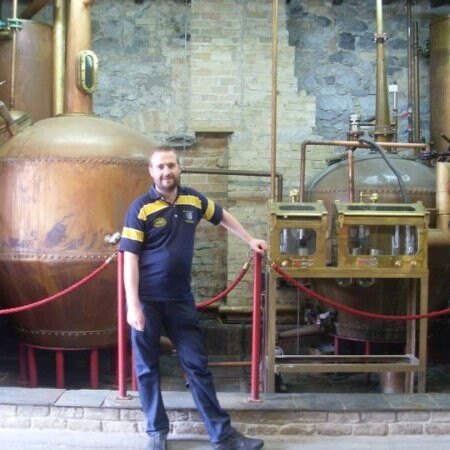
Andrew Watson, Advanced Manufacturing Manager
"The support from the Hartree Centre Northern Ireland Hub has been invaluable in starting our AI journey. The team was fantastic, making complex concepts accessible. I’ve personally gained valuable insights into our data, despite challenges with transitioning to our new ERP system. Huge thanks to Abi and Jade - this has provided us with a great foundation for exploring how AI can further enhance our operations"
Project Impact
The project has provided tangible benefits in operational efficiency as well as data-driven insights:
- Enhanced Quotation Accuracy: The AI-driven model provided precise fabrication time estimates, minimising margin losses and preventing overpricing.
- Optimised Processes: By identifying bottlenecks and workload imbalances, the project reduced downtime and enhanced overall operational efficiency.
- Predictive Capabilities: The Random Forest model accurately predicted fabrication times, with an interactive feature allowing users to input parameters such as output quantity and skill level for tailored predictions.
- Actionable Insights: Visualisation tools, including heatmaps and time-series plots, revealed key productivity patterns and efficiencies, enabling better decision-making and resource allocation.
- Improved Operational Forecasting: The correlation analysis and data visualisation helped to identify key areas for improvement, facilitating more accurate planning and scheduling.
Further Information
This work was completed as one of our data projects. Our projects are up to 12 weeks in duration. We will work alongside your business to scope your project, demonstrate proof of concept, and explore options to deploy it within your business. If you would like to learn more about the Hartree Centre Northern Ireland Hub and our programme, feel free to contact us at: info@hartreeni.uk
Our Impact on UK Industry and Society
The Hartree National Centre for Digital Innovation enables businesses to acquire the skills, knowledge and technical capability required to adopt digital technologies like super computing, data analytics, artificial intelligence (AI) and quantum computing. The SME Engagement Hubs play a key role in offering targeted support for business challenges in their region, creating value and generating economical and societal impact for the UK.
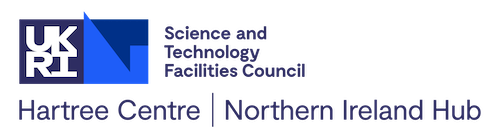
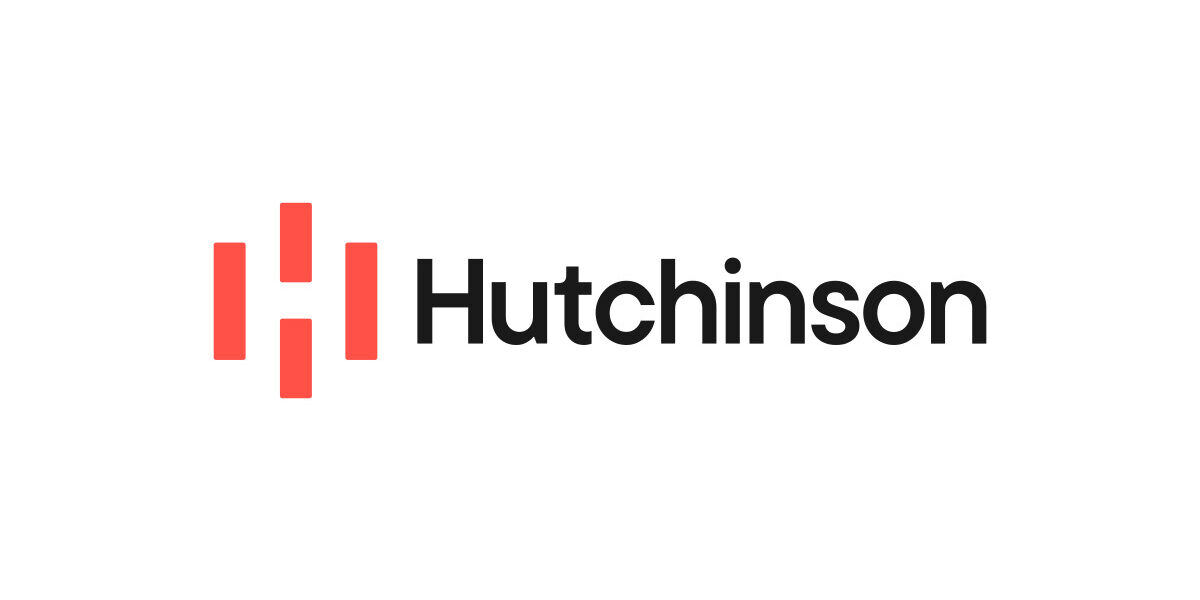